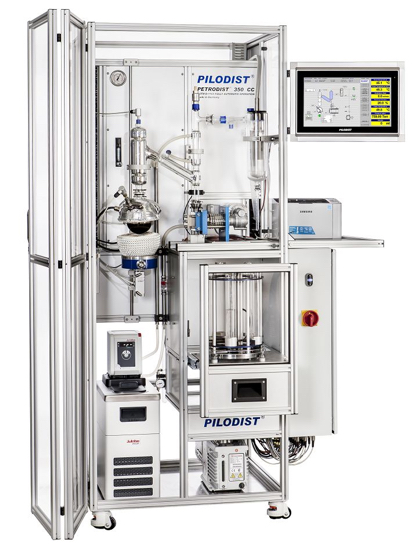
Fully automatic crude oil distillation (ASTM D1160)
Fully automatic crude oil distillation system, processor controlled according to ASTM D-1160 but with automatic fraction collector for the determination of boiling ranges of crude oil products under vacuum. The system can be operated in strict accordance to the ASTM D1160 procedure or alternatively, by using the automatic fraction collector with 5 receivers. The system also provides possibility to work similar to ASTM D5236 and can be optionally equipped with flask sizes of 1000 ml or 2000 ml.
By adding option 1 the system will be also able to do atmospheric distillations of light samples like diesel, biodiesel and charges with water content.
Special advantages of the new PETRODIST ® 350 CC
• parameter input, display as well as calculation of distillation and final data and print out of the distillation curve
• PILODIST IP65 control panel with 15,6” touch screen mounted at the side of framework or alternatively stand alone
as tabletop unit
• easy operation due to user friendly software
• sophisticated safety system
• individual distillation reports and curves can be recalled any time
• precise distillation data due to automatic calculation of the density data based on the receiver temperature
• anti-foaming by dynamic vacuum reduction during evacuation phase
• precise vacuum control by automatic throttle valve
• 2 vacuum sensors (100 Torr and wide range sensor 1000 Torr)
• automatic washing run
• calculation of charge according to receiver temperature and charge density
• quick set up effort as the system is delivered pre-installed
• automatic controlled termination of distillation process and start of cooling
• automatic fraction collector with 5 receivers independent of operation pressure
• new PILODIST-brand fully automatic continuously working discharge (gear) pump
• dynamic vacuum reduction procedure analogue ASTM D5236 (Potstill) is possible
• atmospheric distillation
• water removal (dehydration) process prior to distillation (by adding option 1)
• cutting according to temperature or volume also in different pressure stages
The distillation runs automatically from the initial boiling point to the pre-selected end boiling point or detected
break-off. The criteria for break-off are:
– the pre-selected final AET (atmospheric equivalent temperature) is reached
– the maximum flask temperature is reached
– the pre-selected distillate volume is reached
– the flask insert cracks
– the distillate pressure drops
The distillation volume is measured automatically in receivers, temperature controlled by IR-heater.
The yield is calculated in percentage to the charge quantity. Distillation report, final data and distillation curve
are printed out and stored tamper-proof as pdf file.
A safety enclosure of the system to adequately shield the operator from the distillation apparatus in case of mishap
as suggested by ASTM D1160-15 is quoted as an option as some customers will use the system within a fume hood.
The system consists of:
1 mobile system basis (mounting frame) for the assembly of all parts, equipped with all system specific electric,
mechanic and pneumatic control, mounted on rolls
1 distillation flask, 500 ml, made of glass, with nozzle for temperature sensor
1 flask temperature sensor Pt100 for 500 ml-flask
1 magnetic stirrer bar for intensive mixing of the flask content
1 high-temperature electrical heating bath with insulating mantle for 500 ml flask with temperature sensor Pt100 and
integrated stirrer drive, with lifting platform, heated insulation jacket for the upper half of the flask.
1 distillation head (internal diameter 25 mm) with silvered vacuum jacket, with integrated product cooler, condenser,
the dimensions of the distillation head corresponds to the ASTM-method
1 head temperature sensor Pt100 according to the ASTM-method
1 volume measuring device for the automatic control of the distillation rate with light barrier equipped,
1 light barrier for IBP detection
1 hermetically blocked gear pump for continuous product discharge
1 fraction collector chamber, can heat up to 70 °C with temperature sensor
1 atmospheric automatic fraction collector with 5 calibrated receivers, 200 ml each
1 high precision vacuum sensor, independent of the type of gas, with inconel diaphragm, measuring range 100 mBar
absolute pressure (other ranges upon request)
1 wide range vacuum sensor, independent of the type of gas, measuring range 1000 Torr absolute pressure
1 analog manometer from -1 ... + 0,6 bar for display of actual system pressure status
1 vacuum cold trap for protection of the vacuum pump
1 solenoid valve for vacuum stabilisation with automatic throttle valve
1 vacuum pump, 8 m³/h, 2 stages
1 circulating heating thermostat, 3 l, temperature range +20…+150°C, working range +20°C (ambient temperature)...
+90°C
1 distillation control & data evaluation station 350 CC with PILODIST IP65 control panel with 15,6” touch screen and
printer for input of all distillation parameters and for display of pre-selected, calculated and actual operation values,
with continuous communication to processor, supervising data station. Calculation of the distillation results as well
as printout of yield and distillation curve. Parameters can be stored as recipies and can be reloaded. Results and
distillation curves including oil specific data and laboratory code are stored as .pdf files and can easily be transferred
via network to other users.
Flask charge: 200 mL
Operating temperature: Up to 400° C
Final cut temperature: up to 600° C AET
Max ambient temperature: 25° C
Fraction collector: 5 calibrated receivers, 200 mL each
Operating pressure: vacuum down to 1 Torr
Mains supply: 208-250 V, 50 Hz (standard) /60 Hz (optional)